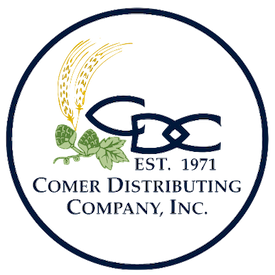
Comer Distributing Co.
Reduces Mispicks, Gets the Crew Home on Time.
Location
Rock Hill, South Carolina
Case Volume
1.8M CE’s annually
The Company
After working as the General Manager of an A-B distributor, Leon Comer acquired the Joseph Schlitz brands from another distributor and in 1971 founded the Comer Distributing Company.
The Challenge
Comer started as a small, 250,000-case operation with only three routes. During the early years, Comer employed five workers; 50 years later, Comer has 78 employees and sells more than 1.78 million cases per year along 14 routes.
Comer’s long history of excellence has allowed the company to build solid relationships with the big players, large chains where pallet mix is expected to be on time and 100% accurate. Usually a piece of cake, order accuracy began to slip as the increased SKU mix and growing order volumes became more challenging to handle with just paper pick sheets from a print kiosk.
“We needed to improve accuracy, plain and simple,” said Brent
Durling, Director of IT and Office Operations. “Mispicks cause
increased work for everyone, and eoPick was easier than we stood the risk of damaging our reputation for quality. Plus, our two warehouse managers were spending hours counting every pallet picked every day just to prevent the wrong product from leaving our warehouse.”
Durling, Director of IT and Office Operations. “Mispicks cause
increased work for everyone, and eoPick was easier than we stood the risk of damaging our reputation for quality. Plus, our two warehouse managers were spending hours counting every pallet picked every day just to prevent the wrong product from leaving our warehouse.”
eoPick came to the rescue. Activated by hands-free voice recognition, eoPick improves the picking process by dispatching pallets wirelessly to the picking crew, increasing speed, accuracy, and safety. For enterprise-level distributors managing thousands of orders a day, integrated palletization capabilities allow distributors to build optimal pallets and loads without the overhead of exports and imports, further reducing costs and increasing productivity.
“What’s more, we’re able to use pickers in other places in the warehouse, wrapping pallets, loading trucks, etc. We run one warehouse shift with eight pickers. In the summer, they worked until 8 or 9, and now they are going home by 6 o’clock. They are hitting their performance goals and receiving incentives for accuracy. It’s a great outcome.”
“Testing and rolling out eoPick was easier than expected,” continued Durling. “It did require us to change our thinking; we didn’t want to automate a flawed process. Instead, we needed to rebuild the process.”
The results are amazing – we’ve reduced our mispicks by more than 90%.
“An individual picker would have 50 to 60 mispicks per week and now they average around 6,“ says Durling. “As a company, we reduced our weekly errors from over 300 to around 25. We now only audit pallets after picking if there is a weight discrepancy; we no longer audit each pallet. That’s a huge time saver.”
Brent Durling, IT and Office Operations, Comer Distributing,
on eoPick
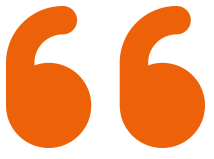
Brent Durling
Director of IT and Office Operations, Comer Distributing
“Testing and rolling out eoPick was easier than expected.”
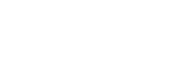
Welcome to eoStar — end-to-end software solutions for direct store delivery distributors.
Products & services
Get in touch
- 1009 Productions Courts Holland, MI 49423